- +1
燈塔工廠觀察|數字化轉型中如何將IT技術納入工業邏輯?
從蒸汽機,到電,到信息技術,工業發展歷經了機械化革命、電氣化革命與信息化革命。2011年,德國提出工業4.0的概念來概括數字化與智能化帶來的制造業變革。
變革的發生往往不是一夜之間的顯著變化,就像15世紀的人們絕不會一天早上打開窗忽然聽到 “中世紀結束”的宣言,它常常是潤物細無聲的。變革也是不均衡分布的,工廠是直觀感受變革的一個絕佳觀察地。
對于當下制造業的變革, “黑燈工廠”、“無人工廠”成為關注焦點,其因機器對人徹底替代的極致性而變成觀看變革的窗口。但這并不是當下存在最普遍的情況,也并非是制造業變革的方向目標。
實際上,從工業邏輯出發,不可忽視的兩個關鍵詞是良品率與成本——盡可能提高良品率與盡可能降低成本。當然,當下而言還要增加“綠色”和“低碳”。
那么具體而言,數字化轉型中如何將IT技術納入工業邏輯,讓數字化轉型安全及“看得見”成效?
“在與亞馬遜云科技的合作中,我們構建了云-邊協同AI工業視覺檢測平臺,實現了產品質量缺陷的智能檢測,將檢測誤檢率降到0.5%內,漏檢率降為0%,實現全自動和智能化,”在施耐德電氣武漢的發展中“燈塔工廠”,施耐德電氣全球供應鏈中國區數字化解決方案負責人冒飛飛分享道。
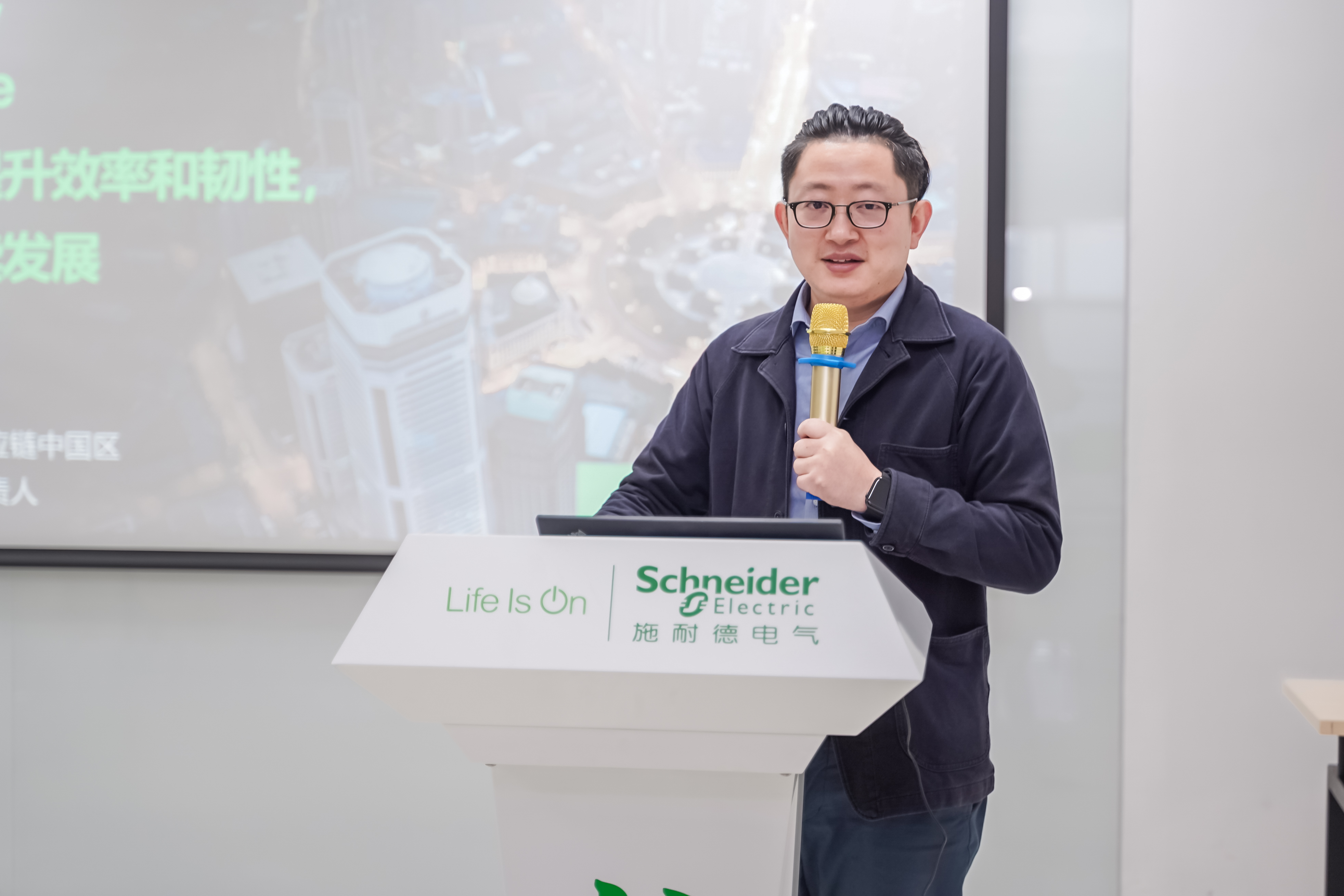
施耐德電氣全球供應鏈中國區數字化解決方案負責人 冒飛飛
施耐德電氣武漢工廠在2018年被達沃斯經濟論壇和麥肯錫從全球工廠中選出,評為發展中的“燈塔工廠”,同年11月被國家工信部評為“綠色工廠”,主要生產微型斷路器、接觸器和其他工業控制類的小元器件,這三類產品的產能目前在施耐德電氣所有工廠中是第一。
施耐德電氣武漢工廠是施耐德電氣全球28家工廠中第一家全面部署EcoStruxure整體解決方案的工廠,在兩年時間內完成了樓宇、配電、機器、工廠、電網五大系統的智能化、物聯網升級改造。工廠里有348個無線電能測量模塊,傳感器實時監測著壓力、溫度、濕度等,能源使用被及時適應性調控,機器設備可以在出現故障前就被及時干預,最后實現了0配電故障停機,以及超過10%的能源優化。
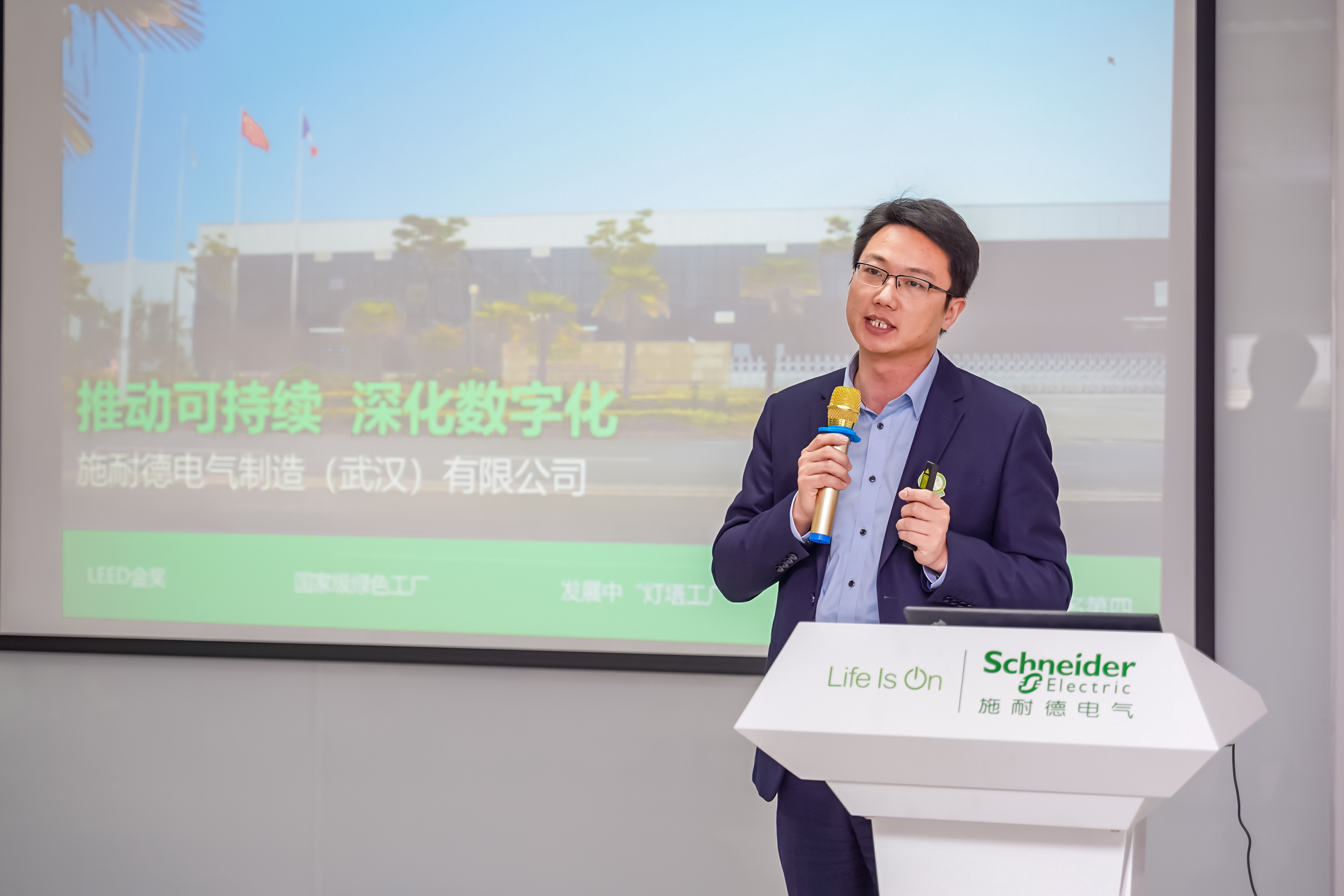
施耐德電氣制造(武漢)有限公司總經理 李聰
“武漢這家工廠的發展歷程可以簡單歸結為三個部分,第一部分是不斷提升內功,提高公司在精益生產和精益運營方面的能力。第二部分是加速自動化的升級改造,第三部分是數字化的轉型,”施耐德電氣制造(武漢)有限公司總經理李聰表示。
冒飛飛則闡述了實現數字化的四維融合,“一是能源+自動化,二是從終端到云,三是從設計與建造,到運營和維護,四是從分散式管理到集成化企業管理。”
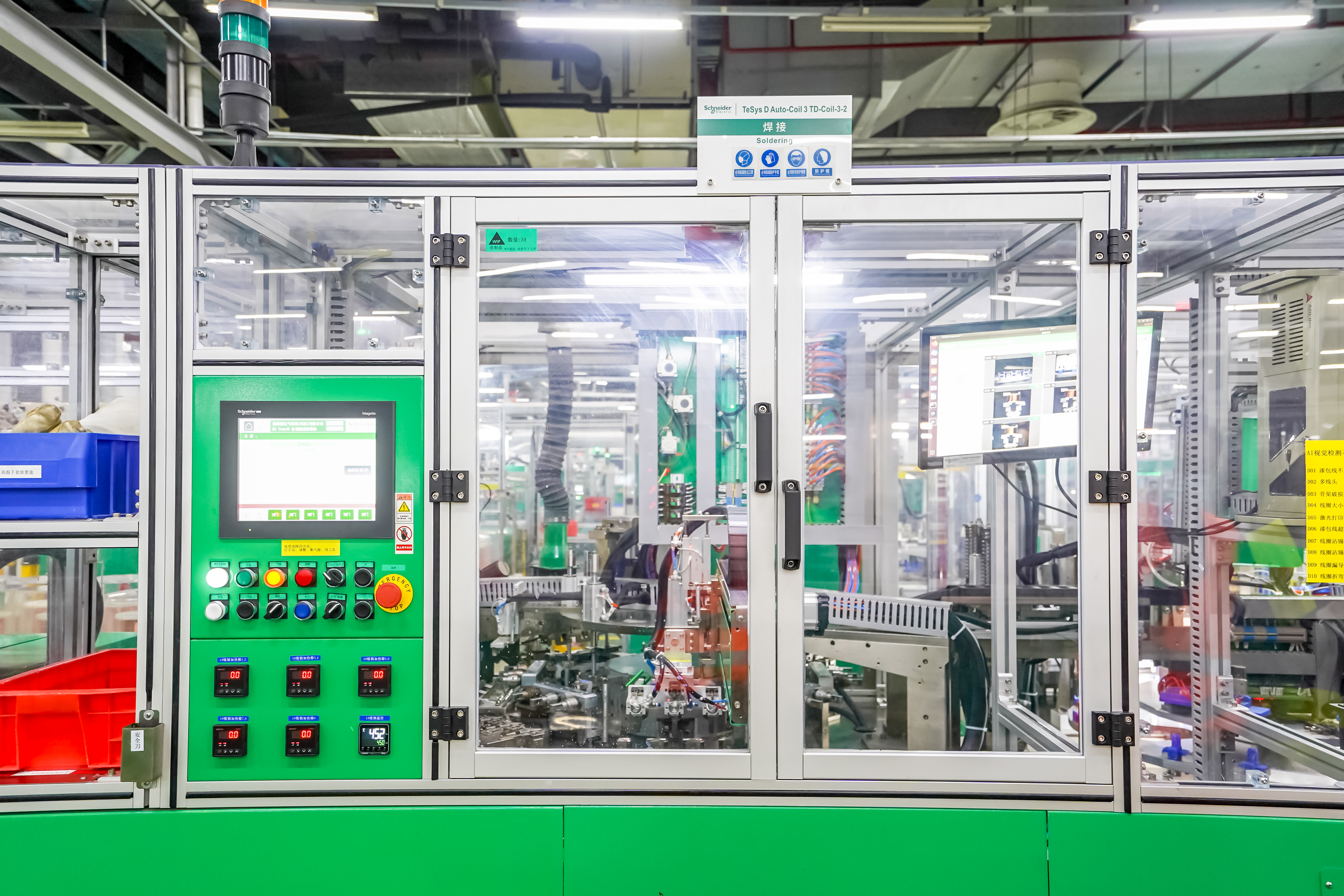
上述所提及的AI工業視覺檢測平臺就是第三部分數字化轉型的重要組成,“在接下來的一年到兩年之內,AI視覺的推廣將是我們的重點之一,”李聰說道。
制造業工廠如何與云廠商合作滿足數字化轉型需要?
武漢工廠所生產的小型斷路器、接觸器等電器部件,在生產過程中會涉及大量的焊接、繞線操作,即便是用全自動化設備,也不可能使液態的焊錫、柔軟的銅絲的厚度、形態完全統一。
那么就需要后續大量的產品外觀質量檢測。曾經使用的是人工目視檢測或傳統視覺檢測(通過生產線上的工業照相機對每件產品進行外觀拍攝,將其與標準樣品對比以判斷其是否有外觀缺陷)。
“傳統的工業制造當中,我們會通過員工每天去看,當這個產品如果一天生產15片的時候,大家看起來可能會覺得比較輕松。如果這個產品一天生產15萬片,如果再去靠人看的話,那么對穩定性和準確率產生很大挑戰,”李聰講解道。
而AI工業視覺檢測平臺可以實現0漏檢,0.5%誤檢率。“0漏檢是件意義非凡的事情,比如用在安全相關的急停按鈕開關,哪怕是0.1%的漏檢率也存在巨大風險,”冒飛飛表示,“為什么我們允許0.5%的誤檢率呢?模型要有非常大量的樣本進行訓練,完全做到0其實非常難。允許0.5%,就是允許可以把好的判成不好的,然后會再檢查一遍,保證檢測精度。”
他認為,成功構建AI工業視覺檢測平臺的關鍵是檢測模型的建模、訓練和迭代。但如果采用傳統的自建服務器方式這里面有兩個問題,“其一是模型訓練和迭代需要巨大的算力,成本非常高;其二是在進行模型訓練時需要工程師到全國各地工廠去采集數據,需要投入大量的人力。”
而后施耐德電氣選擇與亞馬遜云科技合作。
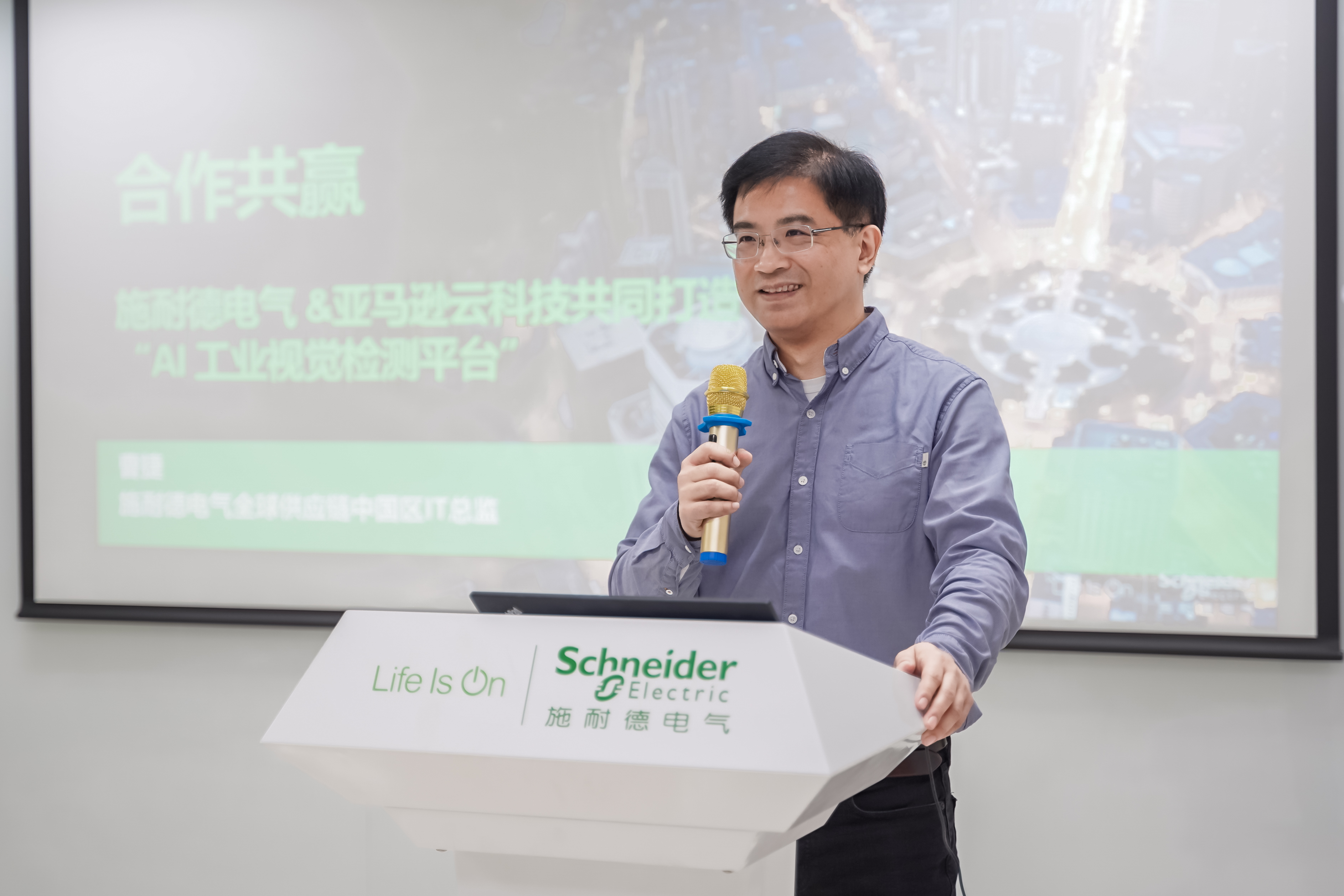
施耐德電氣全球供應鏈中國區IT總監 曹捷
“具體來看,AI工業視覺檢測平臺實際上是一個云邊協同的融合架構,實現云邊端一體化數智閉環的系統。在云端我們可以實現海量的樣本數據的存儲、標注,同時在云端通過Amazon Sagemaker機器學習框架和彈性算力的提供來訓練工業模型,模型訓練好了以后再通過云邊協同的方式,把云端的模型下發到產線邊緣側,執行邊緣推理,并通過產線端的數字化和智能化的改造完成和工業控制元件的集成,從而實現一個整體的閉環回路。”施耐德電氣全球供應鏈中國區IT總監曹捷介紹。
總結來看,就是施耐德電氣收集和提供工業缺陷檢測數據,采用亞馬遜云科技的服務完成包括數據標注、底層機器學習的框架、算力的彈性提供,降低施耐德電氣的算力成本,以及自建模型的框架選擇、數據準備、環境搭建等人力成本。
Amazon SageMaker在單個工具集中提供了用于機器學習的所有組件,從而使用者能以更低成本、更輕松地在更短時間內將模型投入生產。據其介紹,可使企業開發AI模型的三年總體成本降低54%。
目前,這套AI工業視覺檢測平臺實現了產能大幅提升,施耐德電氣已在中國區將其部署到上海、無錫、廈門等地5家工廠的9條產線中,未來還將有8家工廠、44條產線將上線。
從AI工業視覺檢測這一具體的改造方案出發,可以非常清晰地觀察制造業數字化轉型中工業邏輯與IT技術邏輯的互動。
更深度的數字化轉型目標:上下游的協同與需求指導生產
曹捷認為,IT支持的數字化項目的落地和實踐,主要是通過一個兩維的集成框架來推進,“橫向集成指供應鏈價值鏈的集成,主要把核心業務流程數字化,同時把各個業務系統之間的數據勾連打通,從而形成數據驅動的分析、預測和智能決策的能力,提升整個供應鏈的效率和客戶滿意度。縱向集成是以單個工廠的維度、從制造管控的垂直方向,通過施耐德電氣智慧工廠EcoStruxure IoT的解決方案,實現工廠的設備互聯、邊緣控制和在云端的應用和分析。”
李聰更進一步講到了上下游的協同效應,“我們在部署數字化系統的時候,會把上游的供應商也整合進來,比如說它的計劃、庫存、訂單拉動、質量管理等。同時,對于下游的客戶,則是客戶的所有需求、庫存管理以及對客戶滿意度的持續跟蹤。”
以應用場景為例可以更好地理解這樣的上下游協同是如何在一個工廠的體系中具體體現的。
“第一個場景是全球控制運輸塔臺,我們在全球有7個運輸控制塔臺,它負責管理整個運輸環節。這只是運輸環節,我們正在努力打通上下游所有的信息環節,做到端到端的供應鏈的透明度。這意味著客戶在下了訂單以后,他能夠知道的不僅僅是產品的運輸環節,還包含整個供應鏈,包括上游的原材料的準備以及生產的進度,同時還有后端生產完了以后發貨的整個過程進度,這是與客戶端的協同。”李聰對澎湃新聞(www.6773257.com)表示。
他繼續說道,“我們跟上游供應商端的協同有幾個方面,在計劃方面,供應商會知道生產的優先級和排序。在庫存方面,供應商和我們一起找到最合理的、經濟的庫存去提高整個供應鏈的運營效率。我們會在系統平臺上把供應商的庫存納入到我們的管理平臺,一起做計劃,一起做生產的排單。”
第三個質量管理的場景尤為值得注意,“在以前的質量管理思路中,更多的時候我們是被動接收一批原材料,在原材料到達工廠后,我們才能知曉這批原材料的不良比例,從而進行退貨、換貨等。但是現在打通和連接到供應商的整個制造過程中的一些關鍵參數,那么就意味著當原材料的制造過程中出現異常,就會有提前的預警。那么在一批物料有潛在質量風險的情況下,它就不會再送到工廠了。這個過程中,我們就會去分析原因、找到改進措施及替代的方案,來滿足交付和供貨。”
除此之外,據冒飛飛對澎湃新聞記者介紹,重點在做的還有用需求預測指導生產,“從需求端我們可能會用一些AI的方法感知市場上的一些需求,同時結合施耐德電氣本身的一些精益指標去做預測,指導生產。”
吳軍在《智能時代》一書中曾論述道,“生產越來越過剩,需求拉動經濟增長的模式變得不可逆轉。”
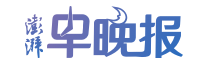
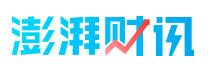
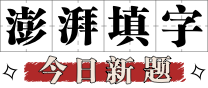
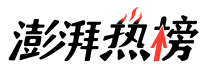
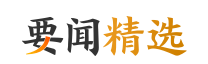
- 報料熱線: 021-962866
- 報料郵箱: news@thepaper.cn
互聯網新聞信息服務許可證:31120170006
增值電信業務經營許可證:滬B2-2017116
? 2014-2024 上海東方報業有限公司